Converting a former industrial plant into a modern office space
Location
Fort Collins, Colorado
Size
101,000 square feet
Empowering employees with choice of workspace
Transforming an aged and stagnant industrial plant into a modern, collaborative corporate office required imagination and innovative design. As a customer-facing space, the REES design team consciously created an inviting and energetic office reinforcing the Fortune 500 Technology Company’s status as a technology giant. Like many of company’s recently designed spaces, the project team played with design juxtapositions that underscore the tech giant’s status as a storied Fortune 500 technology company – coolly cutting-edge and stylishly cultivated.
The Fort Collins consolidation successfully incorporates a hybrid work model that empowers employees with the choice of where and how they work. In addition, textured fabrics, brightly colored furniture and patterned wall coverings introduce an energy to entice employees into the office.
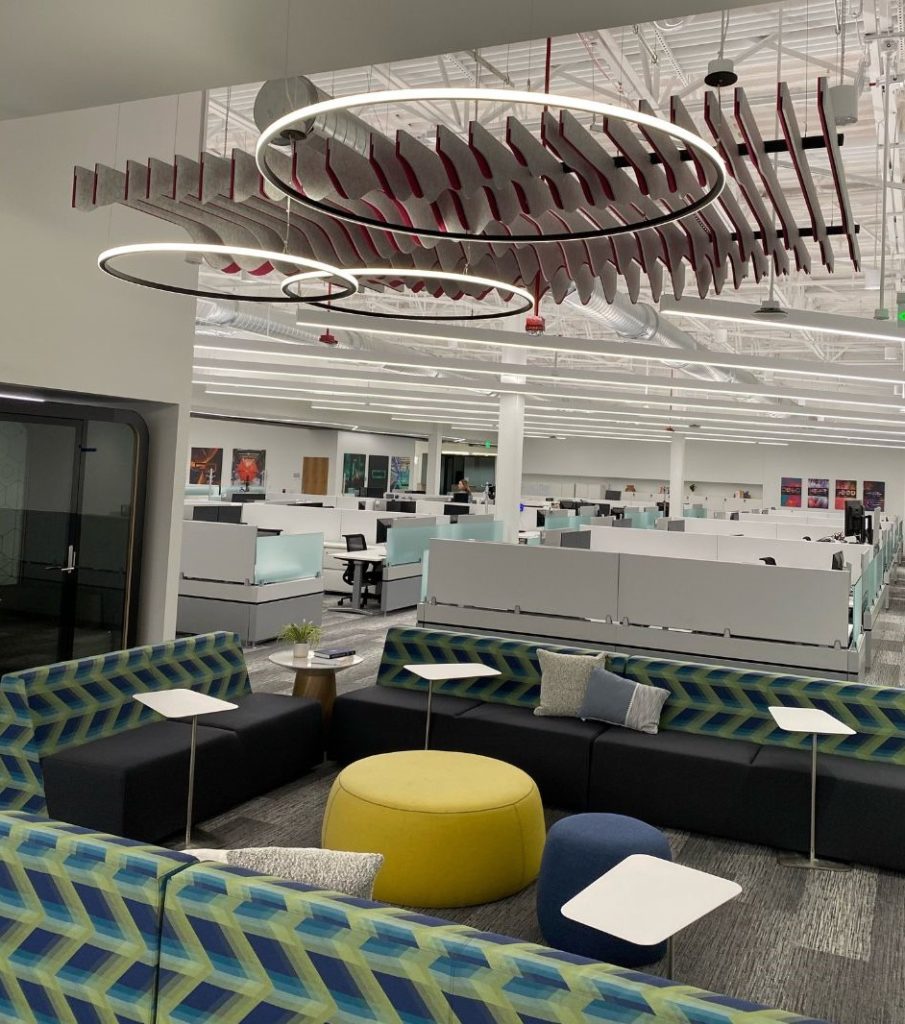
Focused Work
For independent work, employees may choose to focus at individual workstations or opt to use one of the many repurposed focus pods stationed throughout the office space. Cultivating a welcoming atmosphere, the design team added wall coverings behind each focus pod to create an accent of bright colors and interesting patterns.
Casual Collaboration
Carefully curated collections of low-back sofas, colorful pillows and playful modular furniture are strategically placed throughout office as places for casual conversation or impromptu meetings for the engineers. Designed with inviting colors, the employee breakroom is a social gathering space where employees and visitors can opt to work independently or have quick, casual conversations in between meetings. Adjacent to the breakroom is an oversized conference room for more formal meetings. Outfitted with a folding glass wall, the flexible conference room can partition into smaller conference spaces while still feeling open.
Flexible Spaces
The ”Design Studio” is a tailor-made space specially programmed for the engineering team at Fort Collins. Within this flexible space, engineers can arrange furniture in a variety of layouts conducive to their group’s meeting needs. The Studio is equipped with monitors, full-height glass marker walls and sliding marker boards to cordon off space if needed.
Existing Conditions Impact Design
Located within a turn-of-the-century manufacturing plant, the history and uniqueness of the site excited the project team, but also proved to pose some design obstacles.
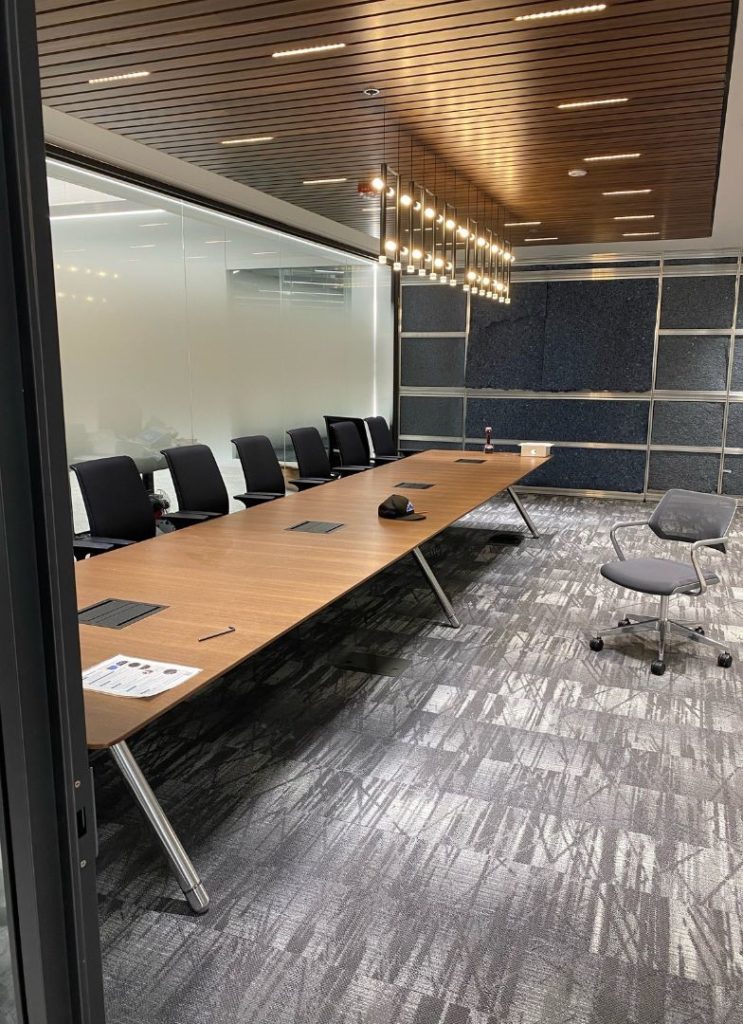
In recent years, this Fortune 500 Technology Company began designing open office spaces to foster team collaboration. Designing a clean, open workspace proved more difficult on this office consolidation. In the middle of demolition, the design discovered an unexpected number of mechanical and electrical systems running the entire length of the former industrial plant. The project team had to creatively incorporate the newly-exposed mechanical items, cable trays and the hundreds of miles of cable into the space’s design to make the elements look intentional.
The REES design team is always conscious to repurpose furniture from former sites. The Fort Collins office consolidation saw furniture being reused from five separate campuses – a logistical exercise in itself. With supply chain affecting ancillary furniture items, the design team had to meticulously curate available furniture that was coordinated, intentional and would arrive on time.
Global pandemic impacts design and construction
The onset of the COVID-19 global pandemic affected the Fort Collins office renovation project. From travel restrictions to supply chain issues, every aspect of how the project was planned, designed and constructed was impacted by the pandemic.
With travel restrictions strictly enforced not long after the project’s kickoff, the design team was only afforded one site visit before planning and design started. Under normal circumstances for a project of this size and scope, the design team would have visited Fort Collins a multitude of times to study and plan prior to drawings being issued.
With only one opportunity to study Fort Collins in person, site issues were discovered in real-time during demolition and construction. This forced the entire project team to address problems contemporaneously as they happened. Problems normally taking a week or two to address were suddenly needing to be solved on site in a matter of hours.
As the pandemic heightened, product availability proved to be scarce and long lead times became more prevalent. Supply chain issues seeped into all realms of the consolidation’s construction pushing the team to make more product substitutions than is typical. To keep construction on schedule, the construction team worked out of sequence to install materials as they arrived.
When supply chain affected the lead time on light fixtures, the project team diligently worked with the supplier to find an appropriate substitute that worked within the scope and design of the space. Despite a backlog of materials and a shortage of labor, the construction remained on schedule and was not negatively impacted.
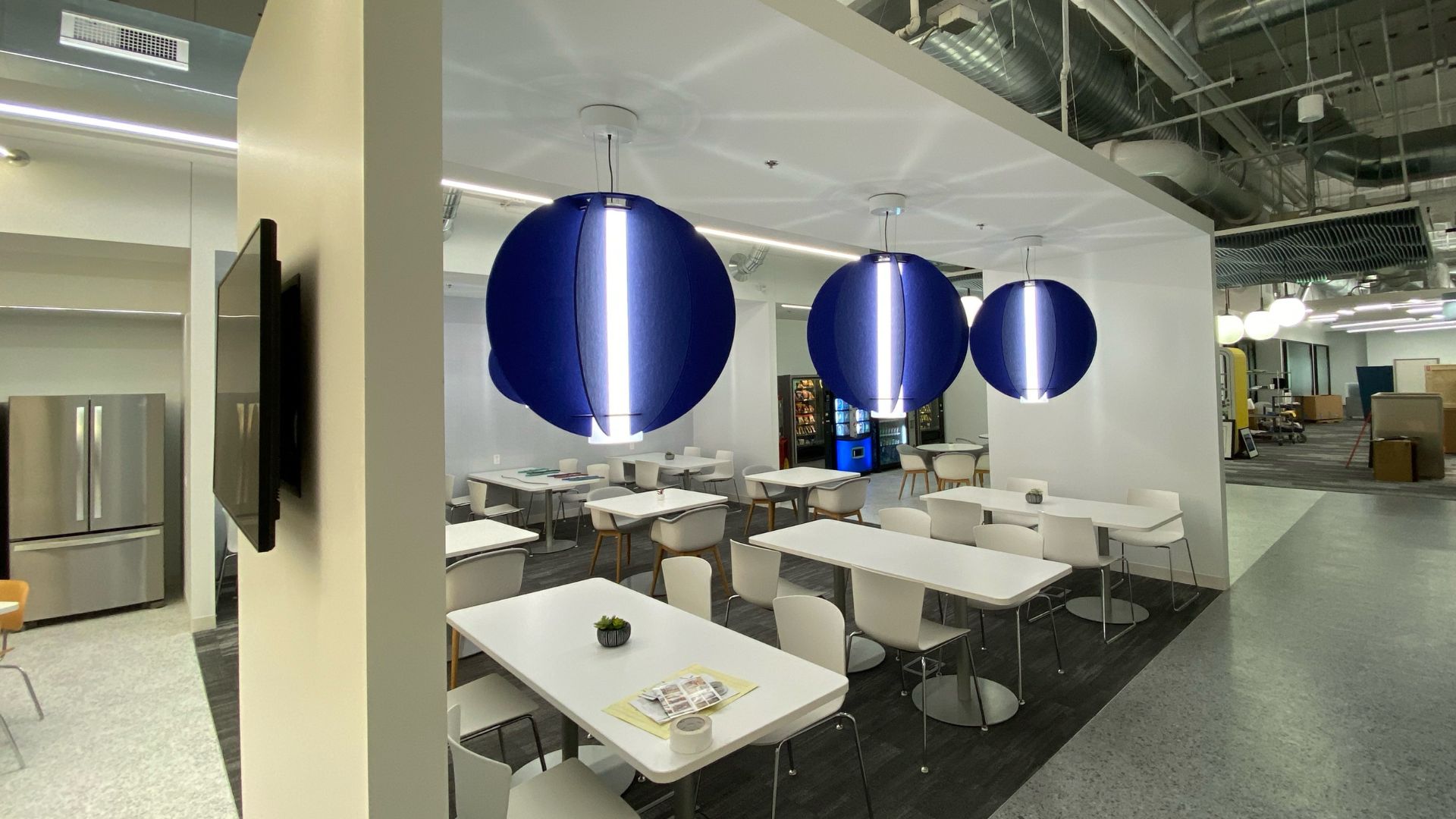